In the field of polymer applications, shrinkage rate is a critical parameter that profoundly affects the dimensional accuracy, performance, and final application outcomes of polymer products.
Whether in everyday plastic items or precision components used in advanced industrial sectors, understanding and controlling the shrinkage of polymer materials is essential to ensuring product quality and functionality.
In this article, we will delve into the key factors influencing polymer shrinkage and explore effective methods to reduce shrinkage.
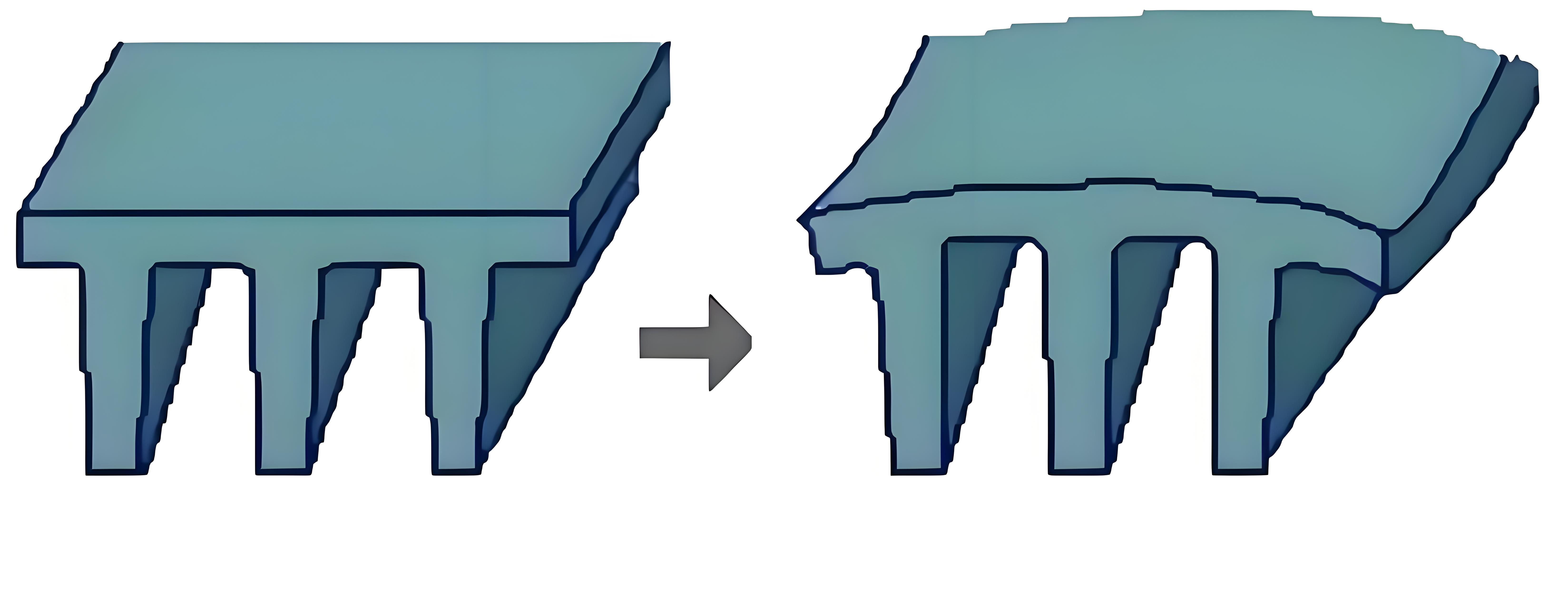
1. Definition of Shrinkage Rate in Polymer Materials
The shrinkage rate of polymer materials refers to the percentage difference between the dimensions of a plastic part at the molding temperature and its dimensions after being removed from the mold and cooled to room temperature. It directly reflects the degree of dimensional reduction of the plastic part after cooling outside the mold.
To illustrate simply, it’s like placing a plastic model at a high temperature into a mold for forming; once cooled, its size will be smaller than its size at the molding temperature inside the mold. This reduction ratio is the shrinkage rate.
The shrinkage rate is calculated by the formula:

where R before is the dimension at the molding temperature, and R after is the dimension after cooling to room temperature.
Due to differences in molecular structure, chemical composition, and other factors, various polymer materials have different shrinkage rates. This makes considering shrinkage rate especially important during material selection and molding process design.
2. Factors Affecting Shrinkage Rate of Polymer Materials
Influence of Raw Materials
1. Different Types of Raw Materials
The shrinkage rates vary significantly among different types of polymer materials.
For example, long fiber-reinforced modified materials typically have a shrinkage rate of approximately 1.2% to 1.5%.
PP homopolymer 40% Long Glass Fiber Reinforced
2. Crystallinity of Raw Materials
When a material has a high degree of crystallinity, its molecular chains are tightly and orderly arranged. During cooling, the chains change from a disordered molten state to an ordered crystalline state, causing significant shrinkage. The tightly packed chains in the crystalline regions reduce the material’s volume, resulting in a higher shrinkage rate. In contrast, amorphous (non-crystalline) materials generally have lower shrinkage.
A simple analogy is stacking wood: randomly piled wood takes up more space, while neatly stacked wood occupies less volume.
3. Molecular Weight of Raw Materials
When the molecular weight is high, the intermolecular forces between chains are stronger, making chain movement more difficult. During molding and cooling, the chains cannot easily rearrange and pack tightly, resulting in a lower shrinkage rate. In contrast, materials with lower molecular weight have more mobile chains that can rearrange and aggregate more easily during cooling, leading to a higher shrinkage rate.
Influence of Molding Process
1. Molding Temperature
Raising the molding temperature increases molecular chain mobility and improves melt flow, allowing more molten material to fill the mold cavity. However, higher temperatures also increase the driving force for shrinkage during cooling. On the other hand, the longer gate-sealing time at higher temperatures allows more melt to enter the cavity, increasing molding density. Overall, the combined effect often leads to a reduced shrinkage rate.
2. Holding Pressure
Higher holding pressure during molding compresses more melt into the cavity, compensating for the volume reduction caused by cooling shrinkage and thereby reducing the shrinkage rate. For crystalline materials, the effect of holding pressure on shrinkage shows a curved downward trend, while for some amorphous materials, the shrinkage rate decreases linearly with increasing holding pressure.
3. Melt Temperature
A higher melt temperature increases molecular thermal motion and improves flowability, making it easier to completely fill the mold cavity. For crystalline materials, it can also influence crystallization behavior, thereby affecting shrinkage. Generally, increasing melt temperature reduces shrinkage, but excessive temperature may lead to material degradation.
4. Mold Temperature
Lower mold temperatures cause the melt to solidify more quickly, shortening cooling time and reducing shrinkage reactions, thus lowering shrinkage rates. Higher mold temperatures slow cooling, allowing more shrinkage to occur.
5. Holding Time
A longer holding time allows the melt to continue filling gaps caused by cooling shrinkage under pressure, reducing the shrinkage rate. However, excessive holding time can increase the molding cycle and may cause stress concentration in the product.
6. In-Mold Cooling Time
For large plastic products with thick walls, sufficient in-mold cooling time is necessary to ensure full cooling and solidification. This helps molecular chains stabilize in their final arrangement, resulting in stable or even reduced shrinkage. Insufficient cooling time may cause continued shrinkage after demolding, leading to dimensional deviations.
7. Injection Speed
For thin-walled products, a higher injection speed allows the melt to quickly fill the cavity, but can introduce higher shear stress, causing molecular chain orientation and anisotropic shrinkage. A slower injection speed may result in uneven filling, which also affects shrinkage.
Influence of Structure
1. Wall Thickness of Plastic Products
An increase in wall thickness slows the internal cooling rate, allowing more complete crystallization and a higher degree of crystallinity, which leads to increased shrinkage. For some amorphous materials, the effect of wall thickness on shrinkage shows no clear pattern.
2. Presence of Inserts in Injection-Molded Parts
When injection-molded parts contain metal inserts, the difference in thermal expansion coefficients between the metal and the polymer can cause uneven shrinkage during cooling, generating internal stress. This may result in non-uniform shrinkage around the inserts, potentially causing warpage, cracking, or other defects.
3. Shape of the Injection-Molded Part
Complex shapes—such as parts with transitions between thin and thick walls, ribs, bosses, or other features—can lead to uneven shrinkage. Thin sections cool quickly and shrink less, while thick sections cool slowly and shrink more, creating shrinkage differences within the same part. Asymmetrical parts are also more prone to non-uniform shrinkage.
4. Shrinkage in the Length vs. Thickness Direction
In injection molding, the molecular chains in the melt tend to be more oriented in the flow direction (length direction), resulting in relatively lower shrinkage. Perpendicular to the flow (thickness direction), the molecular chains are less oriented, leading to relatively higher shrinkage.
Influence of Mold Structure
1. Gate Size
In injection molding, a larger gate reduces melt flow resistance, allows more material to enter the cavity, ensures more uniform pressure distribution, and increases molding density, resulting in a lower shrinkage rate. Conversely, a smaller gate increases shrinkage.
2. Shrinkage in Directions Parallel and Perpendicular to the Gate
In the flow (parallel) direction, molecular chains are more oriented, leading to smaller shrinkage during cooling. In the direction perpendicular to the gate, molecular chain orientation is lower, resulting in greater shrinkage and potentially causing warpage or deformation.
3. Shrinkage Differences Between Areas Near and Far from the Gate
In large molds, areas far from the gate experience lower melt pressure, later filling, and weaker holding effects, resulting in relatively higher shrinkage. Areas near the gate generally have lower shrinkage.
Modification Methods to Reduce Shrinkage of Polymer Materials
Fiber Reinforcement
Taking polylactic acid (PLA) as an example, adding short glass fibers can significantly reduce its molding shrinkage. When the glass fiber content reaches a certain proportion, the shrinkage of PLA composites decreases noticeably. Compared with short glass fibers, long glass fiber-reinforced polymers exhibit even lower shrinkage, with consistent shrinkage in both longitudinal and transverse directions. Whisker-reinforced polymers also show low shrinkage; for instance, PLA reinforced with calcium sulfate whiskers has lower shrinkage than PLA reinforced with glass fibers.
Long Fiber Reinforced Polymers
Inorganic Filler Reinforcement
Filler Shape: In polyhydroxyalkanoates (PHA), platelet fillers (e.g., talc) are more effective in reducing shrinkage than needle-like, granular, or spherical fillers. Platelet fillers form oriented structures inside the material, restricting molecular chain movement and shrinkage.
Filler Particle Size: For the same filler in polybutylene succinate (PBS), smaller particles lead to a greater reduction in shrinkage. Finer fillers disperse more uniformly and interact more strongly with molecular chains, enhancing shrinkage inhibition.
Filler Surface Treatment: Treating calcium carbonate with a coupling agent before blending with PLA improves compatibility, strengthens filler-matrix interaction, and more effectively reduces shrinkage.
Filler Content: In PHA, adding more calcium carbonate gradually decreases shrinkage. However, excessive filler may affect other material properties, so an optimal balance is necessary.
Reducing Crystallinity
Adding Nucleating Agents: Certain nucleating agents in PLA refine crystal grains and lower overall crystallinity, reducing shrinkage. They generate numerous crystallization nuclei in the melt, preventing the formation of large spherulites that cause shrinkage.
Blending with Other Resins: In PBS, blending a small amount of other biobased resins, such as PLA, disrupts crystallization and reduces shrinkage. While the shrinkage reduction effect is smaller than that of fiber or inorganic filler reinforcement, resin blending can improve overall performance.
Blending with Elastomers
PLA can be blended with elastomers such as POE, EPDM, or SBS. When the elastomer content is below 5%, the effect on PLA shrinkage is similar for all types. Above 5%, the effect follows the order: POE > EPDM > SBS, consistent with their toughening efficiency. Combining inorganic fillers with elastomers in PLA further improves shrinkage reduction.
Chemical Crosslinking and Grafting
For PLA, grafting introduces other functional groups or chain segments into the molecular chain, disrupting chain regularity, reducing crystallinity, and thus lowering shrinkage. For polyhydroxyalkanoates (PHA), crosslinking significantly decreases the linear thermal expansion coefficient. Crosslinking restricts chain mobility, so during heating or cooling, chain extension and contraction are limited, resulting in reduced shrinkage.
Polymer shrinkage is a critical parameter influenced by multiple factors. From raw material selection to molding process control, and from product structure to mold design, every stage affects shrinkage. Understanding these factors and mastering modification methods to reduce shrinkage is essential for improving the quality, dimensional accuracy, and performance stability of polymer products.