In today's fast-paced industrial landscape, the demand for advanced materials that offer superior performance and durability is ever-growing. Plastics, particularly in sectors such as automotive, electronics, and construction, are expected to meet stringent stability, heat resistance, and processing requirements. One such solution that stands out is the Styrene-NPMI-MAH Copolymer manufactured by Yangchen Tech, a cutting-edge material known for its exceptional performance as a heat-resistant modifier for ABS (Acrylonitrile Butadiene Styrene) and PVC (Polyvinyl Chloride) plastics.
In this blog, we’ll delve into the unique properties and benefits of Styrene-NPMI-MAH Copolymer and explore how it contributes to enhancing the stability and performance of plastics.
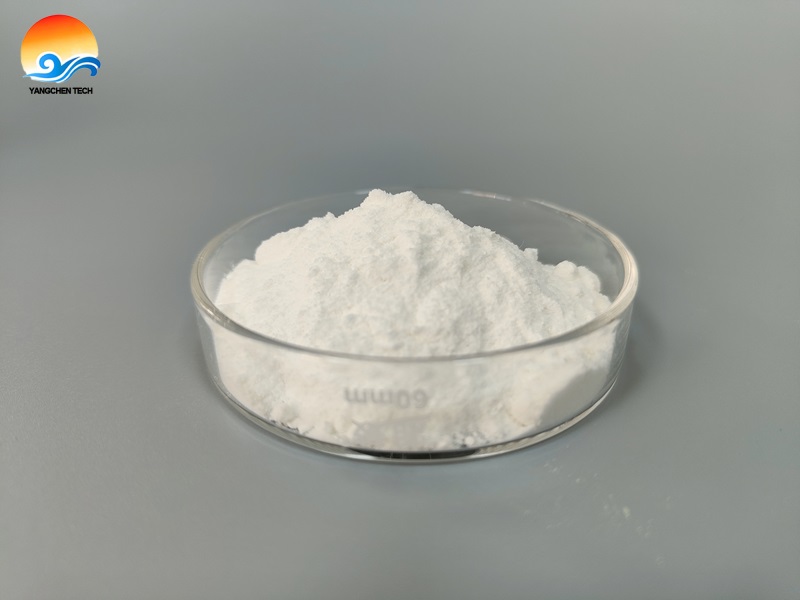
Basic Infomation of Styrene-NPMI-MAH Copolymer manufactured by Yangchen Tech
Test Item |
Test Standards |
Test Data |
Molecular weight and distribution |
GPC |
Mw=12~16*104.PDI=2.0~3.0 |
Glass transition temperature/℃ |
DSC |
160~210℃(Adjustable) |
Initial decomposition temperature/℃ |
TGA |
395-405℃ |
Density |
ASTM-D792 |
1.00~1.15g/cm3 |
Appearance |
NG |
Off-white powder |
1. Exceptional Heat Resistance
Plastics, especially ABS, are widely used in industries where mechanical performance and heat resistance are crucial. However, standard ABS has limitations when it comes to high-temperature applications. The introduction of Styrene-NPMI-MAH Copolymer as a heat-resistant modifier effectively addresses this issue. The maleic anhydride (MAH) and N-phenylmaleimide (NPMI) components contribute to the copolymer's superior thermal stability, allowing modified ABS to maintain its mechanical properties even at elevated temperatures. This enhanced heat resistance makes it ideal for applications such as automotive parts, electrical enclosures, and household appliances.
2. Improved Adhesion and Compatibility
One of the standout features of the Styrene-NPMI-MAH Copolymer is its ability to improve compatibility between different polymer matrices. The maleic anhydride groups present in the copolymer exhibit excellent adhesion properties, making it suitable for blending with other plastics like PVC and even elastomers. This compatibility leads to improved interfacial adhesion, which is critical in composite materials where different polymers are combined to achieve a desired balance of properties. The result is a more robust, cohesive material with enhanced mechanical stability.
3. Enhanced Chemical Resistance
In industries where plastics are exposed to harsh chemicals or environmental stressors, chemical resistance is a critical factor. The Styrene-NPMI-MAH Copolymer contributes to improved resistance against chemicals and solvents, ensuring that the modified plastic retains its integrity and performance over time. This feature is particularly beneficial for applications in chemical processing plants, automotive fuel systems, and construction materials where long-term exposure to chemicals can degrade standard plastic materials.
4. Superior Mechanical Strength
In addition to heat and chemical resistance, the Styrene-NPMI-MAH Copolymer enhances the mechanical properties of plastics. It improves the tensile strength, impact resistance, and dimensional stability of modified ABS and PVC, making them suitable for applications where durability and structural integrity are paramount. Products made from these modified plastics can withstand mechanical stresses without compromising performance, which is especially important in high-impact applications such as automotive components and industrial equipment.
5. Versatile Applications
Thanks to its multifunctional properties, Styrene-NPMI-MAH Copolymer finds applications across a wide range of industries. Some key areas include:
- Automotive: Used in parts that require heat resistance and mechanical strength, such as under-the-hood components and interior fittings.
- Electronics: Ideal for electronic housings that need high thermal stability and chemical resistance.
- Construction: Applied in durable building materials, where both heat resistance and long-term stability are critical.
- Appliances: Utilized in manufacturing household appliances that face thermal cycling and mechanical wear.
As industries continue to demand more durable, heat-resistant, and chemically stable materials, the Styrene-NPMI-MAH Copolymer stands out as a premium solution. Its ability to enhance the thermal, chemical, and mechanical properties of plastics such as ABS and PVC makes it an indispensable material in numerous applications. From automotive parts to electronics and construction, this copolymer significantly improves plastic stability, ensuring products that are not only longer-lasting but also capable of withstanding demanding conditions.
If you're looking to enhance the performance of your plastic products, consider the advanced properties of Styrene-NPMI-MAH Copolymer manufactured by Yangchen Tech for unmatched stability and reliability.