The Low-Altitude Economy
Brings a New Growth Horizon for Carbon Fiber
(1) Carbon Fiber Composites: The Key Material for Achieving Lightweight Aerospace Vehicles
Carbon fiber is a fiber material with over 90% carbon content, featuring numerous properties such as low density, high specific strength, and high modulus. Its tensile strength can exceed steel, aluminum alloy, and titanium alloy by more than 9 times at the same weight, while its elastic modulus can be more than 4 times that of steel, aluminum alloy, and titanium alloy. These advantages make carbon fiber an ideal choice for achieving lightweight in aerospace vehicles. By applying carbon fiber composite materials to the construction of aircraft body structures and internal components, the aircraft’s weight can be significantly reduced, energy consumption minimized, and structural strength and safety enhanced. Using carbon fiber composites in the construction of eVTOLs can help reduce the overall weight of the aircraft by 30%-40%.
(2) The Low-Altitude Economy Brings New Driving Forces for Carbon Fiber Composites
Since eVTOLs, small drones, and some light aircraft are electrically powered, they have even higher requirements for lightweight materials. Carbon fiber composites play a much larger role in the structure and components of eVTOLs compared to traditional aircraft. In the commercial aviation sector, about 50% of the structure of the Boeing 787 is made from composite materials. According to Stratview Research, the proportion of composite materials used in the structure of eVTOLs is as high as 70%. More than 90% of these composites are carbon fiber reinforced, with around 10% being glass fiber reinforced. This implies that carbon fiber composites account for over 63% of the total material used in eVTOLs. In eVTOL composite materials, approximately 75%-80% will be used in structural parts and propulsion systems, 12%-14% in internal structures such as beams and seat structures, and the remaining 8%-12% in battery systems, avionics, and other small applications.
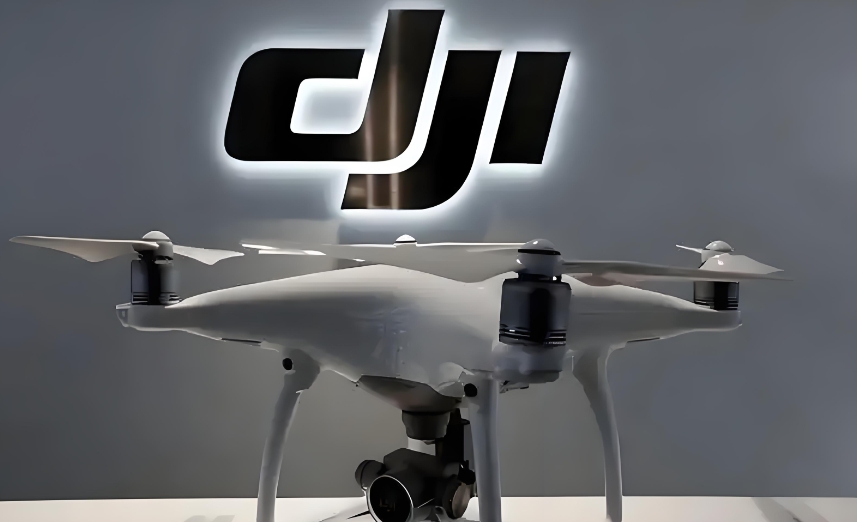
(3) Extensive Use of Carbon Fiber Composites in Mainstream eVTOL Models
The three most mainstream domestic eVTOL manufacturers are EHang, XPeng Aeroht, and Vertical Aerospace. The publicly disclosed models from these companies include EHang's EH216-S, XPeng Aeroht's Traveler X2, and Vertical Aerospace's Shengshi Long. For traditional commercial aircraft, the maximum takeoff weight = empty weight + fuel weight + maximum payload. Since eVTOLs are purely electrically powered, the maximum takeoff weight = empty weight + maximum payload. By subtracting the maximum payload from the maximum takeoff weight, we can estimate the empty weight. According to disclosed data, the maximum individual payload for the Traveler X2 is calculated as (560-360)/2 = 100 kg. Additionally, China Hengrui HRC has disclosed that part of the body of the XPeng Aeroht X2 is exclusively manufactured by HRC, with the carbon fiber portion weighing only 85 kg. Therefore, the proportion of carbon fiber composites = 85/360 = 23.6%. Assuming the eVTOLs from EHang and Vertical Aerospace also use carbon fiber composites at the same proportion of 23.6%.
(4) eVTOLs Will Become a New Growth Driver for Carbon Fiber in the Aerospace Sector
According to Stratview Research, the demand for composite materials in the eVTOL industry is expected to grow substantially in the next six years, increasing from about 1.1 million pounds (approximately 500 tons) in 2024 to 25.9 million pounds (approximately 11,750 tons) in 2030, with a growth rate of about 22.5 times and an annual growth rate of 69%. According to CAO Carbon Fiber's forecast, the demand for carbon fiber in the aerospace sector will increase from 22,000 tons in 2023 to 48,635 tons by 2030, with an annual growth rate of 12%. This forecast does not yet account for the potential boost to the eVTOL industry due to increased policy support. If we refer to these two static projections, by 2030, carbon fiber demand in the aerospace sector from eVTOLs is expected to account for 24.2%. With the acceleration of eVTOL deployment driven by policy catalysts, this proportion could be even higher. It is clear that eVTOLs will become an important source of demand for carbon fiber in the aerospace sector by 2030.
Long Carbon Fiber Composites in the UAV Field
Long carbon fiber composite materials are increasingly being applied in the UAV (Unmanned Aerial Vehicle) field, playing a crucial role in enhancing UAV performance, extending flight time, and improving durability and reliability.
Here are the main applications and advantages of long carbon fiber composites in the UAV sector:
1. Enhancing Strength and Stiffness of UAV Structures
Long carbon fiber composites have extremely high specific strength and specific stiffness, enabling them to bear heavy loads while remaining lightweight. By using long carbon fiber composites in UAV structures such as the fuselage, wings, propellers, and landing gear, the strength and stiffness of the UAV can be significantly improved, ensuring it can withstand complex flight environments and high-speed operations.
2. Reducing Weight and Extending Flight Time
Weight is a key factor that affects the flight time of UAVs. Long carbon fiber composites are extremely lightweight yet offer excellent strength, which helps reduce the overall weight of the UAV. This, in turn, improves battery efficiency and extends flight time. Lightweight design is especially important in small UAVs and electric vertical take-off and landing (eVTOL) aircraft.
3. Improving Impact Resistance and Durability
The high toughness of long carbon fiber composites allows UAVs to maintain excellent impact resistance and durability when encountering collisions or extreme weather conditions. Particularly in the outer shells and critical structural components of UAVs, carbon fiber composites effectively prevent structural damage, reducing maintenance costs.
4. Corrosion Resistance and Environmental Adaptability
Carbon fiber composites have exceptional corrosion resistance, making them ideal for UAVs used in harsh environments such as high humidity or saltwater exposure. This makes long carbon fiber composites a great choice for applications in marine monitoring, agricultural spraying, and other missions requiring strong environmental resilience.
5. Electromagnetic Shielding Performance
Long carbon fiber composites possess certain electromagnetic shielding properties, which help reduce interference from external electromagnetic sources on the UAV's internal electronic systems. This is crucial for the stable flight of UAVs in complex environments, particularly for data transmission and communication systems.
6. Improving Safety
Due to the excellent fatigue resistance and aging resistance of carbon fiber composites, they effectively extend the lifespan of UAVs, reducing the risk of failure due to material degradation. This contributes to improved flight safety.
Application Examples:
Small Consumer UAVs: Many high-end consumer UAVs, such as certain models from DJI, have begun using carbon fiber composites in their body structures, particularly in wings and support frames, to enhance flight performance and durability.
Military UAVs: Military UAVs, which require high durability, strength, and stealth capabilities, widely use long carbon fiber composites. These materials not only reduce weight but also enhance structural strength and stealth features.
Electric Vertical Takeoff and Landing (eVTOL) Aircraft: eVTOLs have extremely high requirements for weight reduction. Long carbon fiber composites are ideal structural materials for eVTOLs. By using these materials, eVTOLs can achieve lightweight designs while ensuring sufficient strength and stiffness, thereby improving range and flight efficiency.